ゴムの成形
~金型の種類や構造 成型方法と問題点~
ゴムを製品形状にするためには金型が必要です。
ゴム部品の形状に合わせて金型を製作し、成形を行います。
ここではゴム金型の種類や成形方法、成形後の製品の仕上げ方法、ゴム製品で見られる不良とその対策のノウハウについて紹介します。
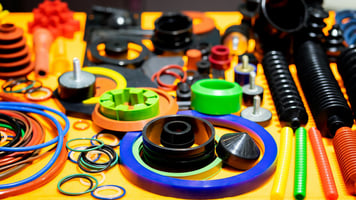
ゴムの成形方法と金型構造
◆直圧成形
直圧成形はコンプレッション成形、べた押し、とも呼ばれます。
ゴム材料を直接キャビティ(製品になる部分)に仕込み、圧力をかけてプレスし成形する方法です。構造がシンプルなので比較的安価に金型を製作することが可能です。分厚い製品は材料不足の不良を起こしやすく、厚み方向の寸法精度を出しにくいデメリットがあります。
◆直圧成形型の構造
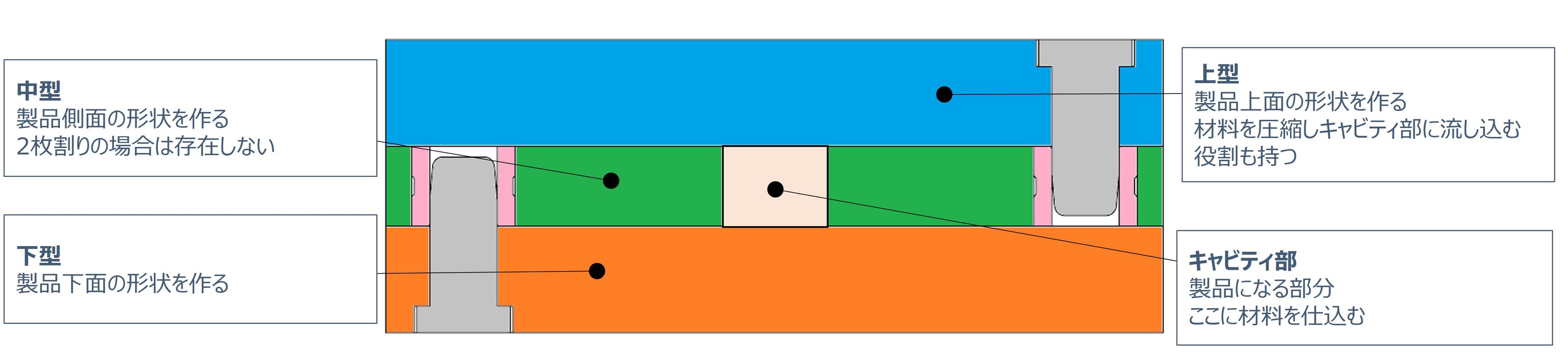
◆注入成形
注入成形はトランスファー成形とも呼ばれます。
ポットと呼ばれる部分に材料を仕込み、圧力を掛けゲートからキャビティ部に材料を流し込み成形します。直圧成形金型と比較して厚み方向の寸法精度を出しやすい点が特徴です。また仕込み材の重量管理幅や形状管理幅が直圧成形金型より広いです。一方で材料のロスは多いです。
◆注入成形型の構造
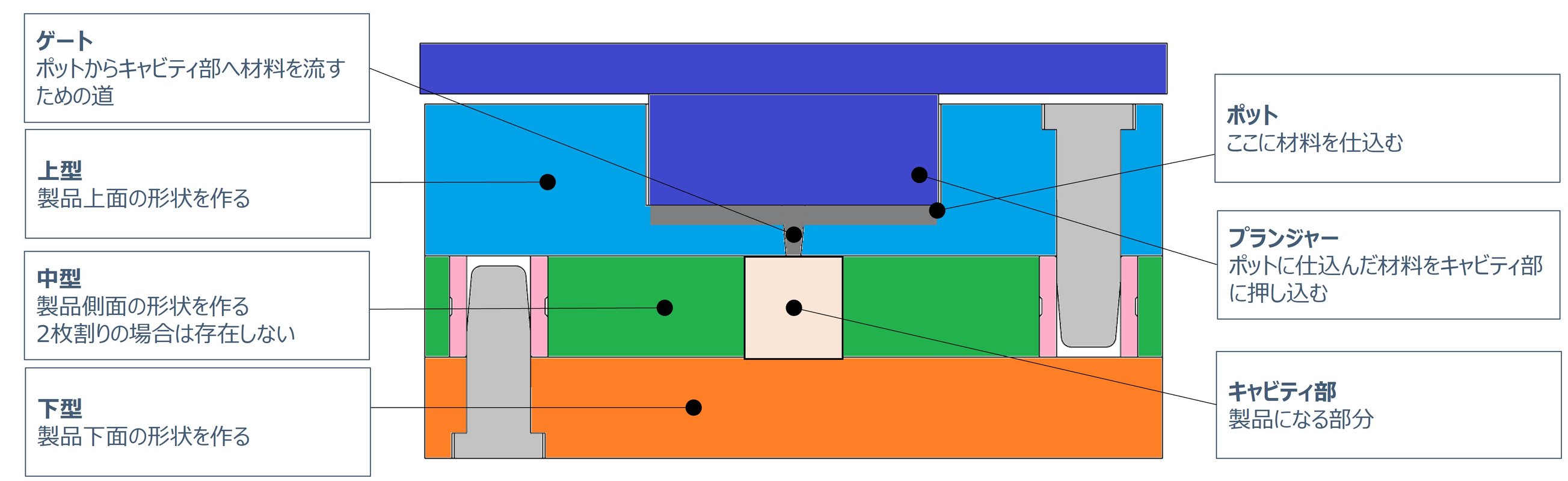
◆射出成形
射出成形はインジェクション成形とも呼ばれます。
材料は成形機からランナーを介してキャビティ部に流し込んで成形します。製品の形状によっては無人で生産する事が可能ですが金型のコストが直圧成形、注入成形に比べ高くなります。
下記イラストはコールドランナータイプです。
◆射出成形型の構造
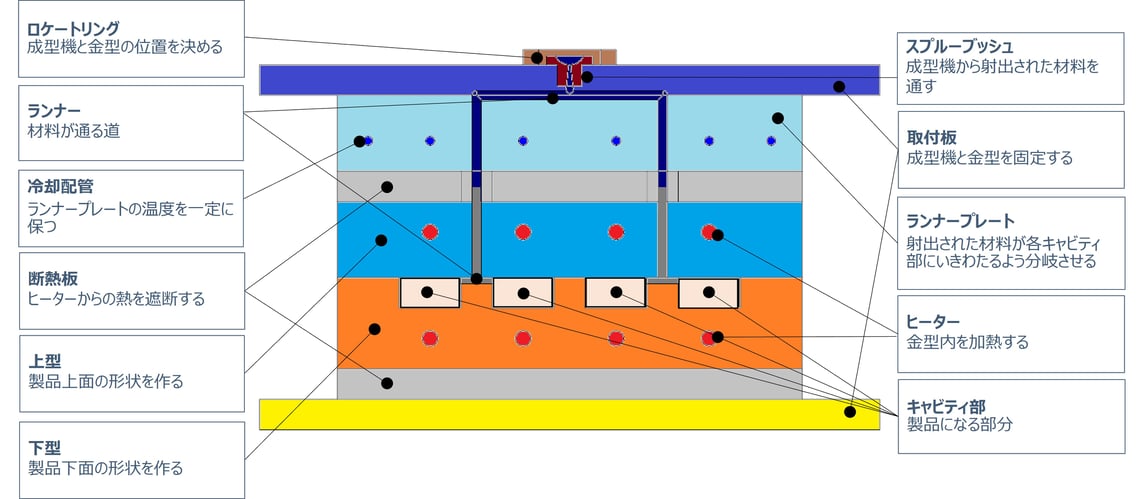
ゴム製品の仕上げ
成形が完了した直後のゴム製品はバリが付いている状態です。
発生したバリと成形品を分離させる事により製品として完成します。ゴム製品の仕上げ方法として代表的な手法を紹介します。
◆手仕上げ
仕上作業者が手作業で製品からバリを除去する仕上げ方法です。喰い切りを手で引っ張り製品からバリを除去して仕上げていきます。
この場合、金型には喰い切り溝の設定が必須になります。

◆抜きポンチ
製品形状に合わせた抜きポンチを製作し、抜きポンチの刃で製品とバリを分離させて仕上げる方法です。
この場合、抜きポンチの刃で製品とバリを分離させる為、喰い切り溝の設定は不要となります。
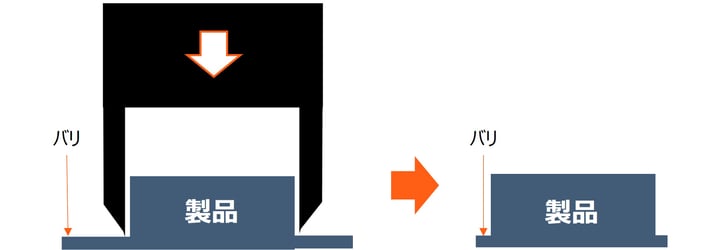
◆抜き仕上げ型
専用の抜き仕上げ型を製作して製品とバリを分離させます。
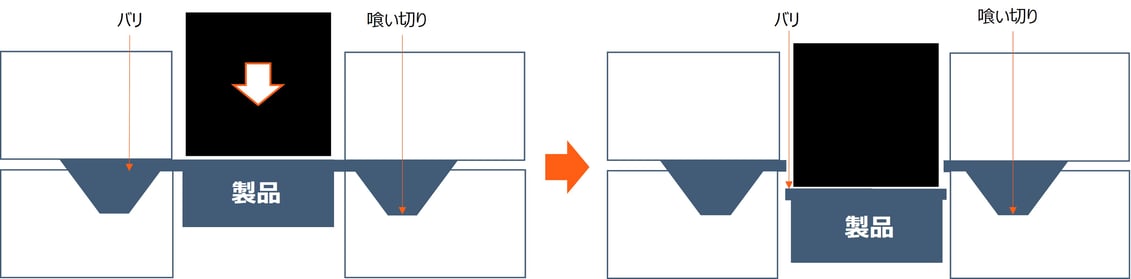
ゴム製品で見られる不良現象
◆ヒケ(バックラインディング)
型割部やゲート部が変形(凹み、盛り上がり)している
キャビティに材料が充填した後も過剰な成形圧力がかかり続けると、型割部やゲート部付近の加硫しかけた材料が無理やり動かされ、その部分に融合不良や収縮差による変形が発生することがあります。
成形圧力(加硫している間の圧力)を低くすることで改善されることがあります。
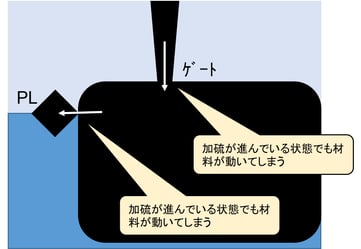
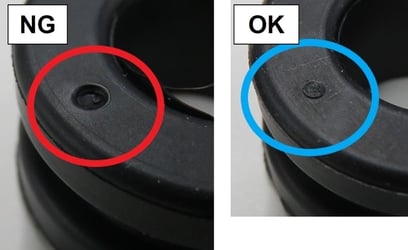
◆材料不足(欠肉、ショートショット)
キャビティに材料が充填されていない
慢性的に発生している場合
成形圧力不足(成形圧力に対し過大な取り数や型サイズである)、ゲート位置形状・設置数が不適切・材料重量・材料仕込位置、材料仕込形状が不適当・材料の流動性が悪い。
この場合 成形条件、設備、金型仕様等を見直す必要があります。
突発的に発生する場合
材料スコーチによる流動性の悪化、ゲート詰りが発生してしまったことが考えられます。
この場合 材料のスコーチ具合、金型の確認等が必要となります。
.jpg?width=190&height=250&name=%E3%82%B7%E3%83%A7%E3%83%BC%EF%BE%84%20%E6%9D%90%E6%96%99%E4%B8%8D%E8%B6%B3(%E5%A4%A7).jpg)
.jpg?width=450&height=250&name=%E3%82%B7%E3%83%A7%E3%83%BC%EF%BE%84%20%E6%9D%90%E6%96%99%E4%B8%8D%E8%B6%B3(%E5%BE%AE).jpg)
◆融合不良(ウェルド)
材料融合部が割れている、スジが見える
材料不足により融合部に圧力が加わらず密着不良になることがあります。また、圧力がかかっていても離型剤や仕込材表面に析出した薬品が融合面に集まり融合阻害を起こすことがあります。
材料不足が原因の場合は前出の材料不足対策を実施。融合阻害を起こしてるもの(離型剤、配合薬品等)が原因の場合は、それらの見直しが必要です。
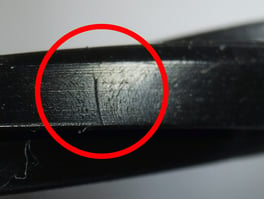
◆エア(バブル)
製品内部や表面に膨らみ(断面は空洞)がある
製品形状、型割位置等により、キャビティ内の空気や材料から発生したガスが抜けず膨らみができることがあります。
この場合 成形条件調整や金型構造の見直し、場合によってはエア発生部にエア逃がしの形状を追加する必要があります。
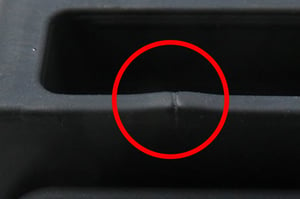
◆発泡
製品内部や表面に膨らみ(断面は空洞)がある
加硫中に発生するガスは加硫が進むに従い増大するゴム材料の強度によって押え込まれていきますが、加硫不足の場合、発生ガスの圧力に負けてガスがつぶしきれないことがあります。
金型温度が伝わりづらい肉厚形状内部や材料が金型に入るタイミングが遅いゲート付近に発生することが多いです。
金型温度を上げる、もしくは加硫時間を延長することで対策します。
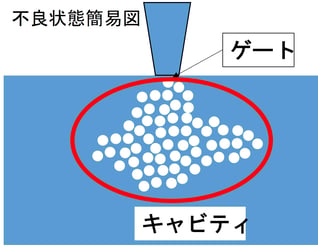
◆欠け(割れ、破れ、裂け)
製品の一部が欠損、破損している
成形時に発生している場合
高温時のゴム材料は室温の時より伸びが短くなっており、脱型時の変形により破損しやすい状態にあります。特に無理抜きになっている部分や応力集中しやすい部分は破損が発生しやすくなります。また、混入した異物や分散不良資材が起点となる場合もあります。
この場合 材料の変更や成形条件の変更が考えられます。また、金型の調整や離型剤等を使用することで改善されることがあります。
仕上げ時に発生している場合
脆い材料を使用している製品では喰い切り仕上げが安定せず製品の一部を抉ってしまうことがあります。
この場合 手仕上げから抜き仕上げ等の別の仕上げ方法へ変更することが考えられます。
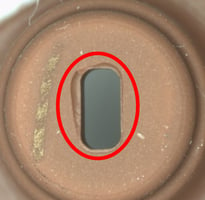
◆変形
製品がゆがんでいる
成形時に発生している場合
無理抜き脱型、スコーチ材混入、脱型直後の製品積み重ねによる変形が主な原因です。対策として脱型補助治具の使用、加硫温度を下げるなどの成形条件調整が考えられます。
保管時に発生している場合
長期間の製品積み重ねによる変形と考えられます。
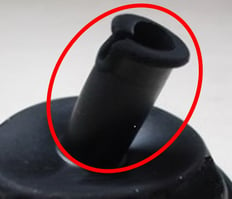
◆異物混入
製品表面や内部に異物が入っている
異物の混入経路としては主に次の3点が考えられます。
①配合資材そのものに混入②混練り時に拾い込む③混練後に材料表面に付着する。
異物混入を防ぐには作業環境の4Sが必要です。
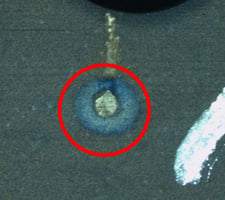
◆バリカミ
製品にバリが混入している
金型の清掃不足により金型内に残っていたバリや他の成形工程から飛来したバリ等がキャビティ内に入り込み発生します。
バリカミを防ぐには金型清掃手順の変更や作業環境の4Sが必要です。
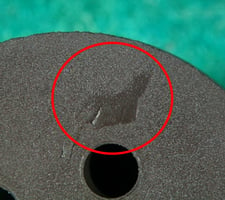
◆ヤケ(別称:スコーチ)
製品表面に凸凹がある。もしくは爛れたような表面になっている。
スコーチ材が混入すると製品表面が均一でなくなってしまうことがあります。スコーチ材は材料保管によって発生するものと成形時に発生するものがあります。
材料保管で発生するスコーチは保管環境や有効期限の見直しが必要です。成形時に発生するものは成形条件調整の他に材料の置き方や仕込み作業時間の短縮なども考える必要があります。
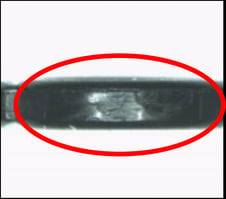
◆型傷
製品表面に凸※となった異常部がある⇔型汚れ
金型の表面異常が製品に転写されたものです。
金型に原因がある為、特定キャビ、特定箇所に恒久的に発生します。
表面異常としては 金型加工痕、金型取扱中についた打痕や引っ掻き傷、金型腐食により発生した欠孔等が考えられます。この場合、金型修正が必要になります。
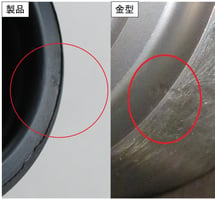
◆型汚れ
製品表面に凹み※となった異常部がある⇔型傷
金型に付着した汚れが製品に転写されたものです。
材料そのものや材料から析出した物質、離型剤等が金型表面に堆積し汚れとなることが多いです。
金型洗浄が直接的対策になりますが、金型表面処理、離型剤使用により汚れが金型表面に堆積しにくくなることもあります。
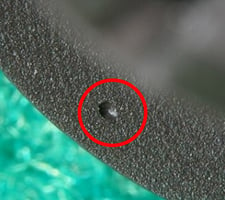
◆ブルーム/ブリード
ブルーム:製品表面に粉が噴き出す現象
ブリード:製品表面に液状物が滲み出ている現象
ゴムの配合資材が表面に析出してくる現象です。
ブルームの場合、析出してくるものは主に、加硫剤系薬品、老化防止剤系薬品などが多いです。
ブリードでは油状添加物が表面析出しています。
対策として材料面では配合薬品の変更や添加量調整、加硫条件や保管条件、製品の取り扱い方法の変更で軽減されることもあります。
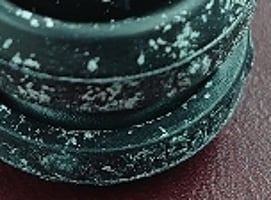
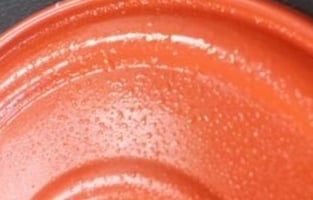