ゴムの混練
~配合剤とゴム材料の混練方法について~
ゴムの混練りとは?
ゴムは原材料であるポリマーを配合資材と混ぜ合わせ、練り込むことでゴムの性能をより引き出すことができます。このゴム材料を混ぜ合わせて練り込む工程をゴムの混練りと呼びます。
混練りは、配合設計に従いポリマーと配合資材を均一に混合分散させたコンパウンドを得る工程であり、ロールやニーダーといった混練機を用いて練り込みます。
混練りは工場での製造ラインでゴム製品の品質に関わる最も重要な工程であり、もし混練り工程でミスが生じれば後工程に大きな影響が及びます。そのため、混練りはゴム配合の通りに、各種材料を練り込まなければならない重要な工程となります。
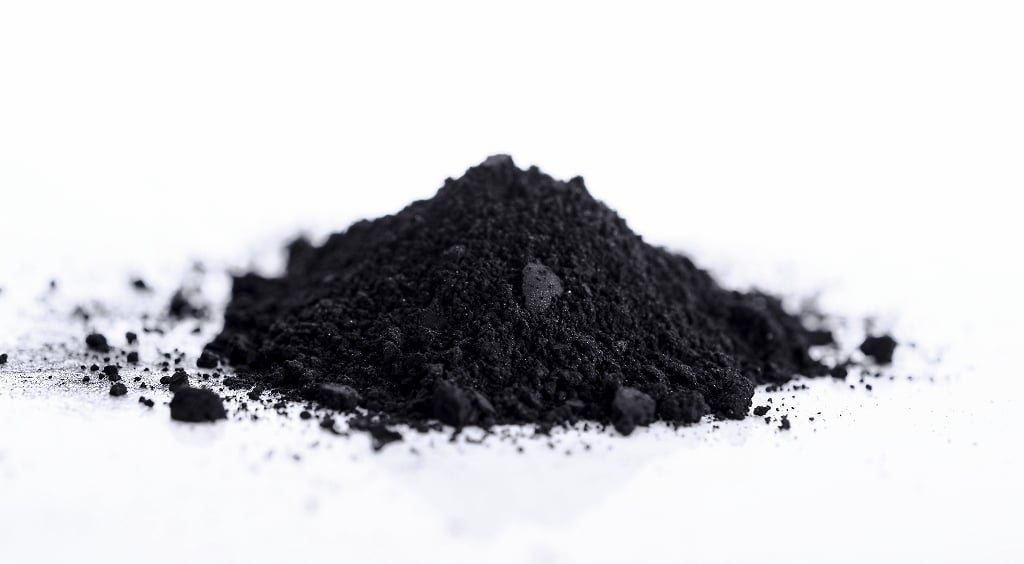
ゴム練りの工程
ゴム練りは大きく分けて、素練り、混練り、分出しの3工程があります。
ここではロール練りの映像と合わせて説明します。
①素練り工程
素練り工程では、ポリマーのみを混練機で練り込みます。
オープンロールでの素練りは、ブロック状のポリマーをロール間に通し、段々とロール間隔を狭めて薄く伸ばしていくことでロールに巻き付けます。
ポリマーにせん断力を加えることで材料粘度を下げ、弾性が強い状態から可塑化させ配合資材を練り込みやすい状態にします。
②混練り工程
混練り工程では素練りしたポリマーに各種配合資材を練り込んでいきます。
一般的には、加硫剤以外の補強剤、可塑剤、加工助剤、老化防止剤を先に練り込み、最後に加硫剤を練り込んでいきます。また、材料の分散を促すため、切り返しを行う必要があります。
ただし、配合資材の添加タイミングや量、練り方は一定の基準があるわけではなく、目的の特性を得る練り方などを模索する必要があります。
③分出し工程
分出し工程は、練り込んだゴム材料を目的の大きさで排出する工程です。
分出しは加圧ニーダーでは行えないため、オープンロールで行います。
ロール幅や、間隙を調整することで後工程に対応した幅、厚みでのゴムコンパウンドの排出が可能です。
混練りに使用される配合資材
ゴムの配合資材は多種多様あり、目的としたゴム特性を目指して、対応する資材を配合・調整し材料開発を行います。
配合資材の種類は、ポリマー、補強剤、充填剤、可塑剤、加硫剤、老化防止剤などがあります。
ポリマー
ゴムの原材料。ポリマーがゴムの特性に大きく関与する為、用途に対応したポリマーを選択し使用します。
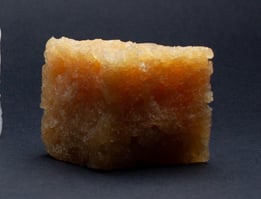
補強剤
ゴム特性の硬度、引張強さ、弾性といった物理特性に変化を与えます。
入れるほど硬く、強くなりますが、伸びにくくなる傾向がみられます。カーボンブラック・シリカなどの種類があり、粒径や比表面積によって得られる特性が異なります。
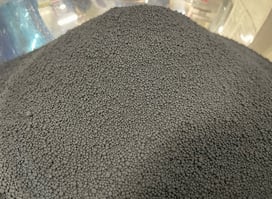
充填剤
炭酸塩、ケイ酸塩が主に使用されており、シート加工時の押し出し、表面肌に改良がみられます。
増量剤としても使用されますが、入れすぎは練りや成形時に影響を及ぼします。
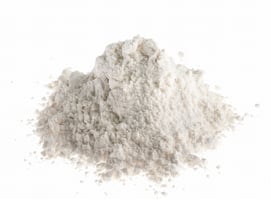
可塑剤
分散性と流動性、低温性などの改良や硬さの調整に用いられます。
鉱物油や植物油があります。ただし、使用する場合はポリマー等との相溶性や加硫阻害が起きる可能性を考える必要があります。
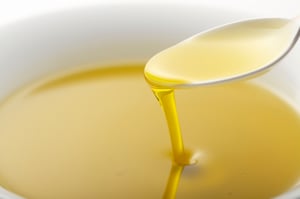
加硫剤
ポリマーを加硫させてゴムとします。ポリマーの化学構造に対応した加硫剤が使用できます。
硫黄系では炭素間二重結合のあるポリマー、有機過酸化物系はそれに加えて二重結合をもたないポリマーも架橋が可能となります。
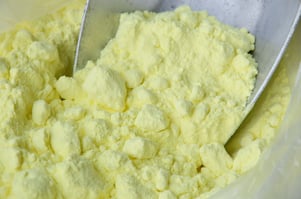
老化防止剤
ゴム製品は製造から劣化が開始しゴム特性に影響を与えます。
ゴムは、酸素・オゾン・熱・光・動的疲労などの要因による劣化を受けやすいため、対応する各種の老化防止剤を少量練り込みます。
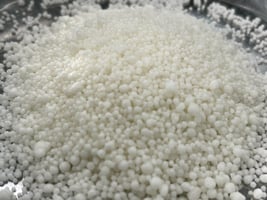
混練機の種類と特徴
オープンロール
オープンロールは、人により作業が行われるため練り込み速度が他の混練機と比較して低速になります。また開放系であることから、混練り中のゴムコンパウンドの熱の上昇が抑えられます。
そのため、ロール間隙のせん断力が他の混練機と比較して大きくなり、分散が良くなる傾向があります。オープンロールでは熱がかかりにくいことから、加硫剤も練り込めます。また、後工程で使用するようなシート状やリボン状に分出しが可能です。
短所としては一度に練る容量が少なく、作業時間もかかるため、生産性が悪いことが挙げられます。
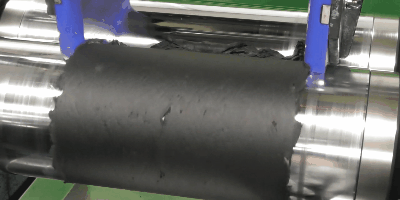
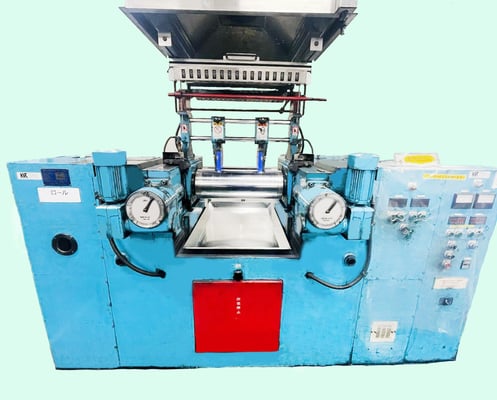
加圧ニーダー
加圧ニーダーは最も一般的な混練機です。
材料がローター、混合槽の壁面の間などで練り込まれることで発熱し、混合槽内が密閉空間であることからオープンロールでの練り込みに比べ、高温での練り込みが可能となります。
大型機であれば一度の練り容量も大きいため、生産性が上がります。オープンロールに比べると、粉末材料の飛散の抑制や作業時の安全性は高いです。
また、ブレード形状は接線式で、2つのブレード間で回転速度が異なります。
しかし、加圧ニーダーは他の混練機に比べると冷却性能が劣るため、混練温度が高くなり過ぎるとせん断力の低下が起き、添加資材の分散が悪くなる傾向があります。
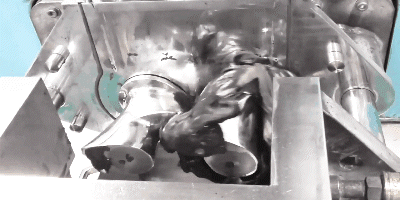
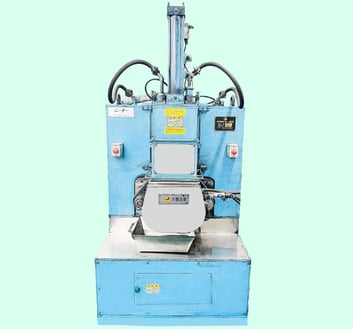
インターナルミキサー
インターナルミキサーは加圧ニーダーと類似しており密閉空間での加圧練り込みとなっていますが、ブレードが異なり噛み合い式となっています。
噛み合い式のブレードは接線式に比べブレード径が大きく練り込みが効きやすく、材料とブレードの接地面積が広いため加圧ニーダーよりも冷却効率が良好な傾向にあります。
しかし、短所としては、ニーダーよりも生産性が低くなります。また、混合槽の容量が加圧ニーダーと同じであっても、混練機自体のサイズが大きいため、加圧ニーダーに比べより広い設置スペースを必要とします。
バンバリーミキサー
バンバリーミキサーは加圧ニーダーと類似しており密閉空間での加圧練り込みとなっていますが、高馬力での高速練り込みが可能で大量生産に特に重点を置いています。また、材料投入口は上部にあり、練込み後のゴム材料は混練機下部から排出されるため、その後の練工程に効率よく移行することが可能です。
しかし、高馬力での高速練りを実現する為、混練機自体の大きさや投入口の高さにより設置が難しいといった課題もあります。
また、混合槽内の清掃が難しいため、コンタミが起きる可能性やメンテナンス性が悪いです。
参照:
ポスティコーポレーション ゴム材料技術 配合創り・練り手順と技能・不良対策 大坪一夫 著
新版ゴム技術のABC 第2版 編集・発行 社団法人 日本ゴム協会東海支部