ゴムの材料特性
~各種類ごとの特徴紹介と検討事例~
ゴムの素材は様々です。用途にあったゴム製品を作るには材料選びがとても重要です。ここでは各種ゴムの特徴・長所・短所についてと実際にゴムの特性を生かしたゴム材料の選定事例についてご紹介します。
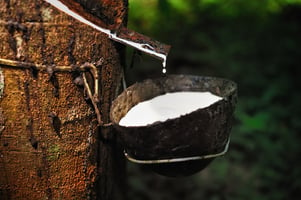
ゴムの材料の種類と特徴
天然ゴム(NR)
天然ゴムはゴムの木の樹液から得られるラテックスを加工したものです。そのため天然ゴムはバイオマス由来のゴムになります。優れた機械的強度のある特徴からタイヤや、日用品では輪ゴムに使用されています。
・長所
機械的強度が高い
耐摩耗性、反発弾性、電気絶縁性に優れる
・短所
構造に二重結合を持つことから耐熱性、耐候性が悪い
加工時に素練りによる可塑化が必要
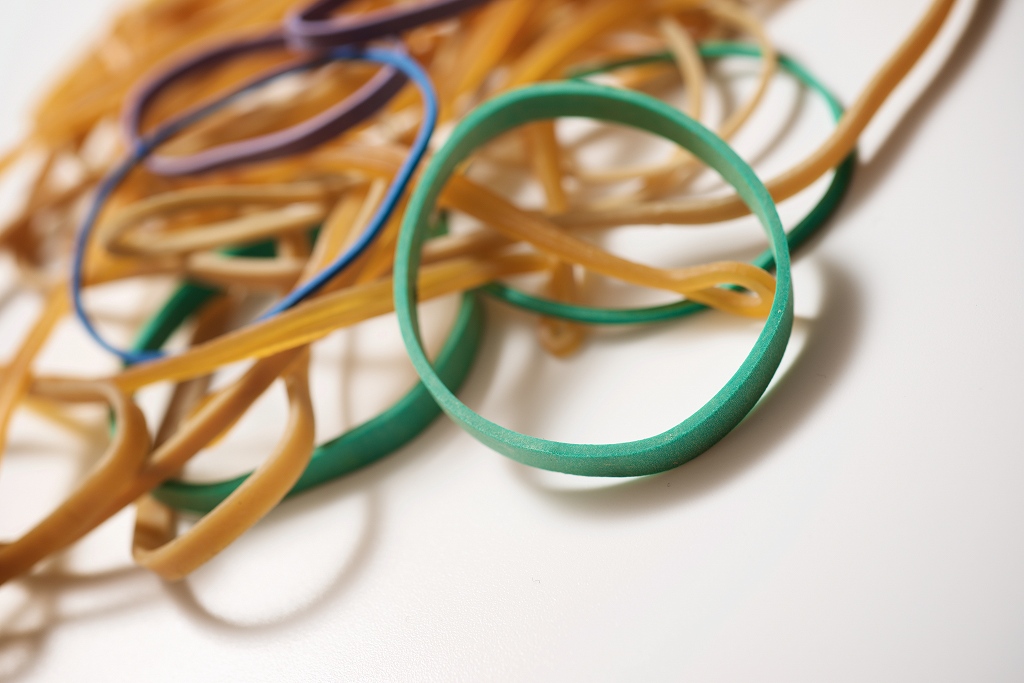
ニトリルゴム(NBR)
NBRは主鎖に二重結合を持つジエン系ゴムの中で最も耐油性に優れているゴムです。
その優れた耐油性からオイル周りのホース、ガスケット、シールなどに使用されています。
・長所
ニトリル基の極性に由来する高い耐油性
・短所
構造に二重結合を持つことから耐熱性、耐候性が悪い
耐寒性に劣る
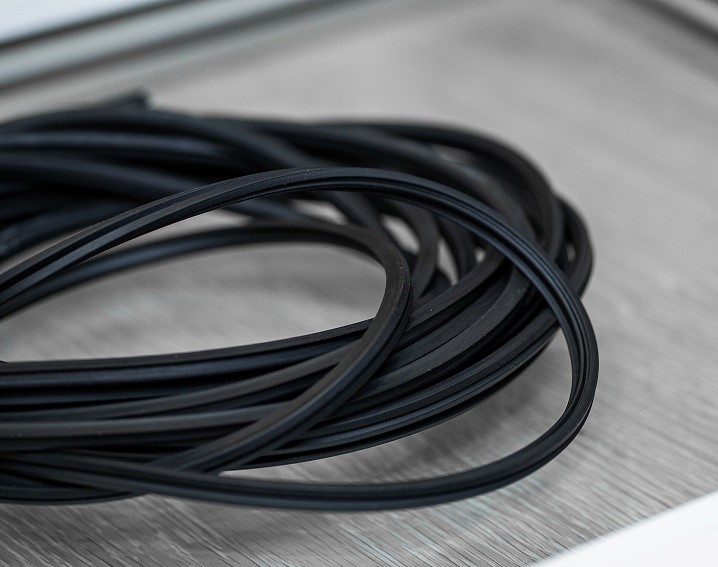
水素化ニトリルゴム(H-NBR)
H-NBRはNBRの主鎖に水素を導入し、不飽和度を高めたゴムです。NBRから主鎖の二重結合が減ることで物性が大きく改善されます。
耐油性に加え、耐熱性が要求される部品で使用されています。
・長所
NBR同様に高い耐油性
NBRと比較して、耐熱性、耐候性、耐摩擦性の向上
・短所
NBRよりコストが高い
耐寒性に劣る
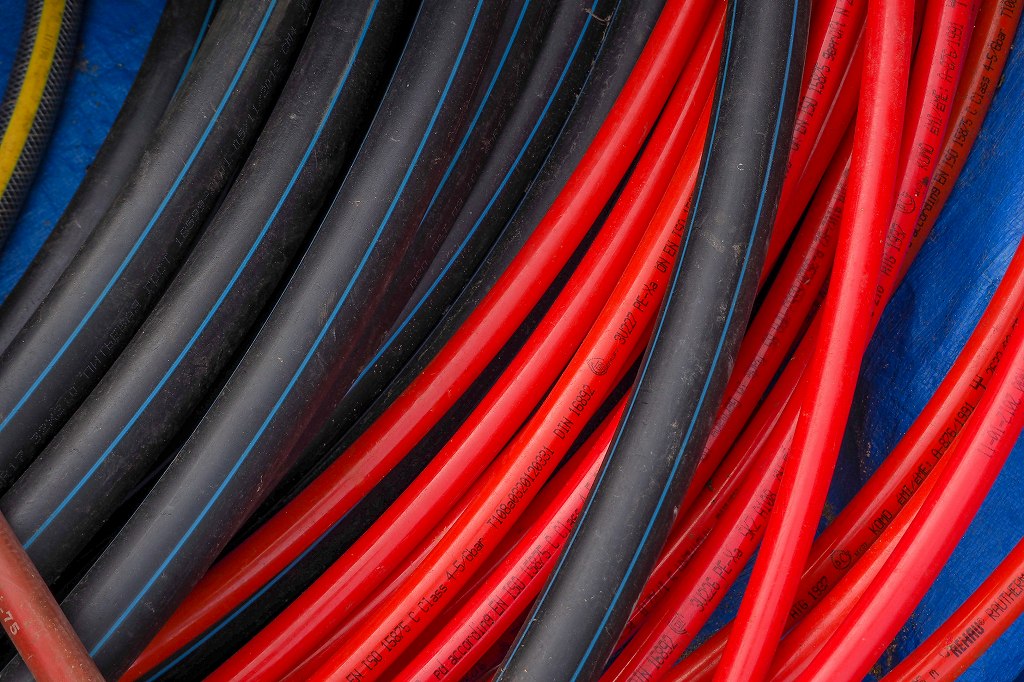
フッ素ゴム(FKM)
FKMはポリマー内にフッ素を含有し、様々な特性が高水準なゴムです。
自動車のエンジン周りや化学プラントといった耐熱性、耐油性、耐薬品性などが同時に求められる環境で使用されています。また、比重が大きいという特徴があります。
・長所
耐熱性、耐油性、耐薬品性にとても優れる
・短所
コストが特に高い
耐寒性に劣る
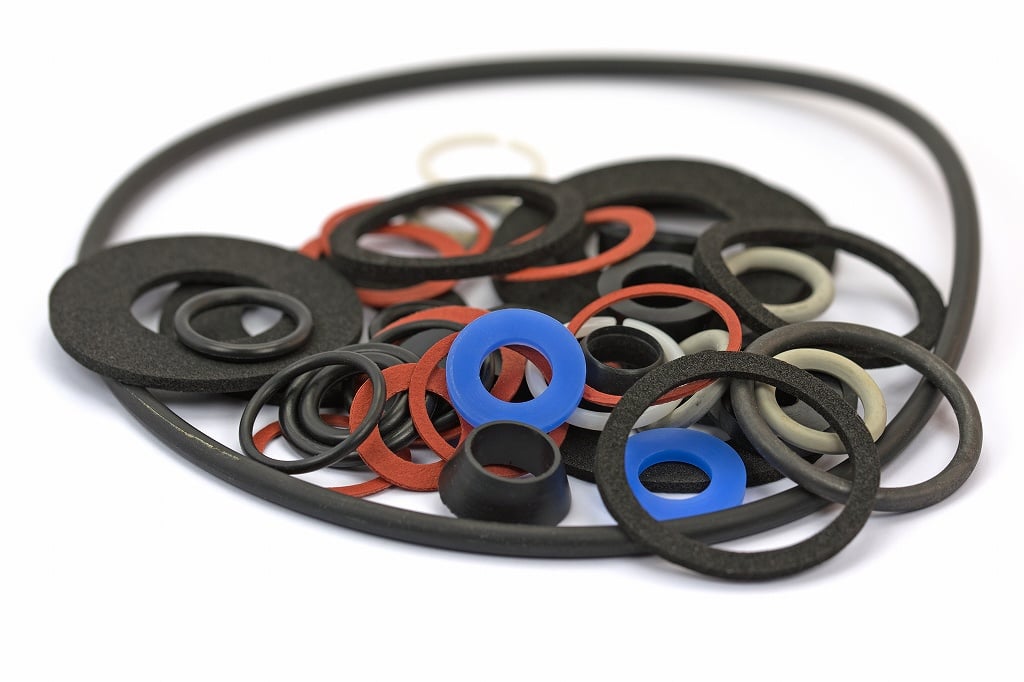
シリコーンゴム(Q)
シリコーンゴムはシロキサン結合(-Si-O-)を主鎖とするゴムで、人体への影響が少ないため、医療用ゴム栓などに用いられているという特徴があります。
・長所
耐熱性、耐寒性、耐候性に優れる
人体に安全である
・短所
耐引裂き性や耐摩耗性に劣る
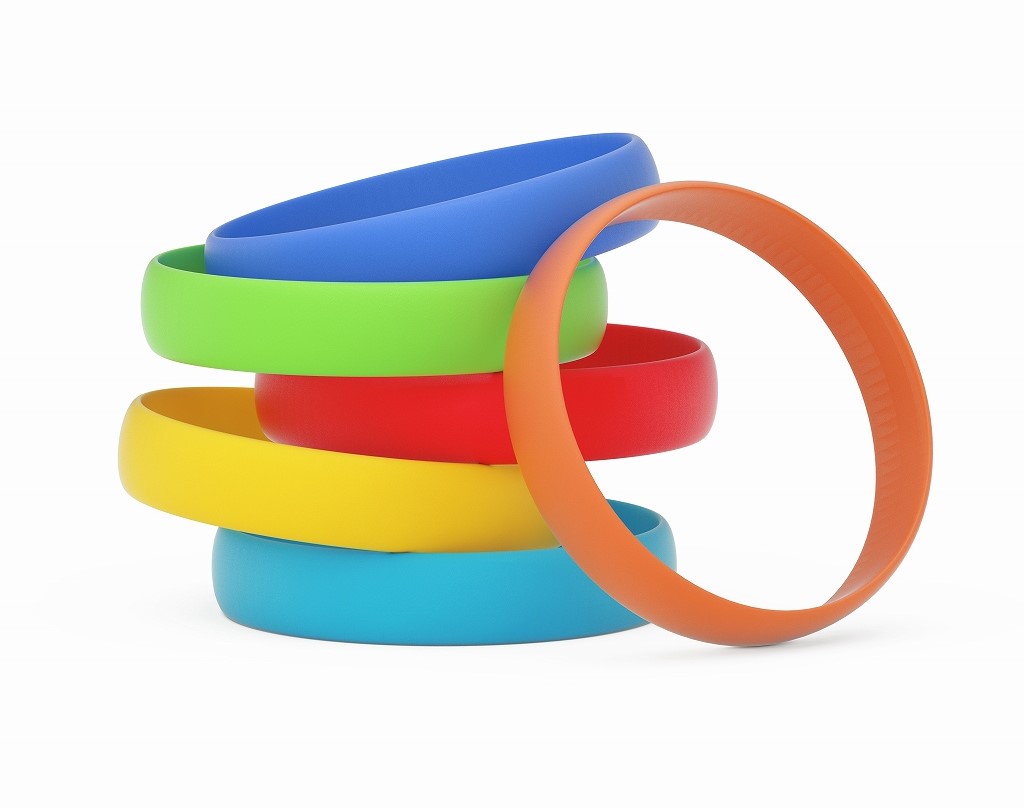
エチレンプロピレンゴム(EPDM)
EPDMはエチレン、プロピレン、ジエンの三元共重合によって得られるゴムです。
主鎖に二重結合を持たないため、耐熱性、耐候性がよく、自動車部品のほか建築用シートや電線被覆などで用いられています。また、比重が小さいという特徴があります。
・長所
耐熱性、耐候性、耐オゾン性に優れる
・短所
耐油性に劣る
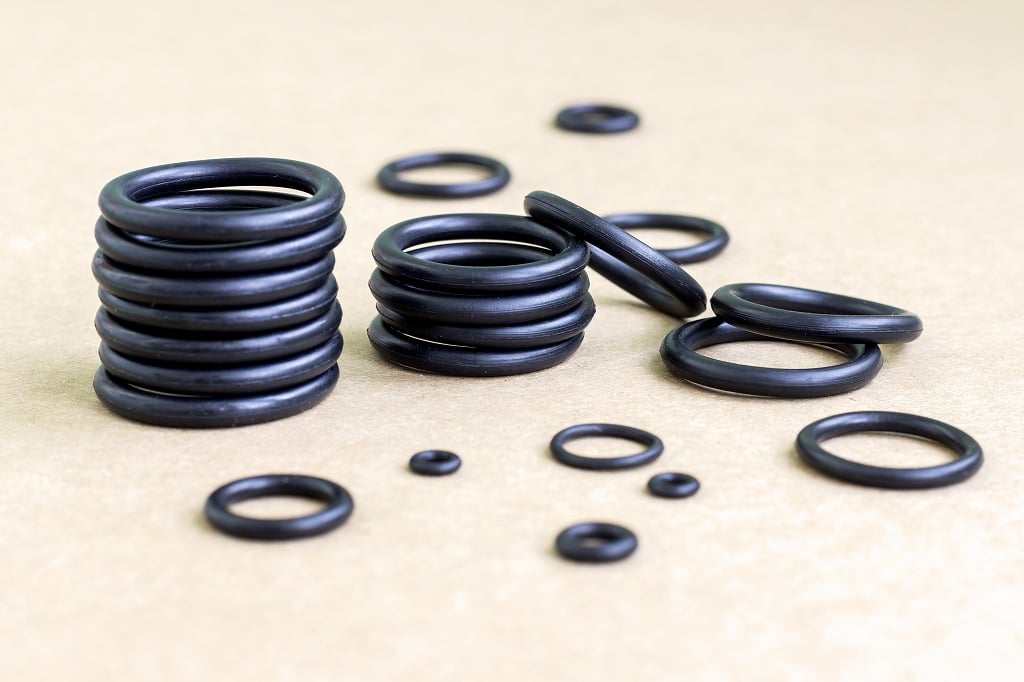
クロロプレンゴム(CR)
CRは物性のバランスが良いところが特徴で、要求項目の多い自動車部品や耐候性が必要な電線、接着剤としての利用など様々な製品に使用されています。
・長所
機械的強度、耐熱性、耐薬品性、耐候性についてバランスよく優れている
・短所
耐寒性に劣る
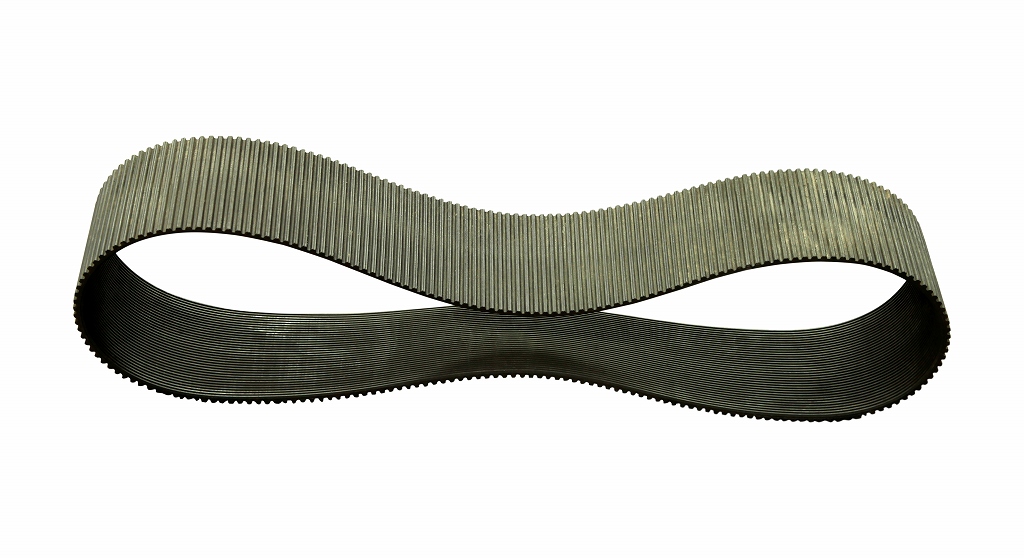
アクリルゴム(ACM)
ACMは種々のアクリル酸エステルからなり、耐熱性と耐油性に特化した性能を持つゴムです。耐熱性と耐油性の両方を求められるオイルシールなどに使用されています。
・長所
耐熱性、耐油性に優れる
・短所
機械的強度、耐寒性に劣る
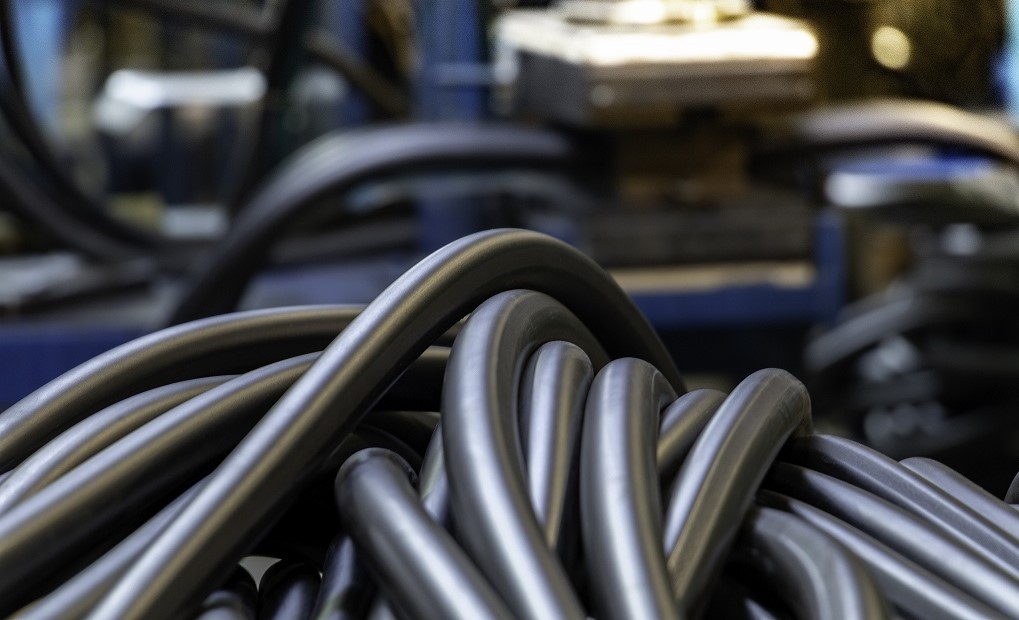
ブチルゴム(IIR)
IIRはイソブチレンと少量のイソプレンから合成されるゴムで、極めて低いガス透過性と低い反発弾性が特徴です。その特徴をいかして、タイヤのインナーチューブなどに用いられています。
・長所
極めて低いガス透過性
電気絶縁性に優れる
・短所
耐油性に劣る
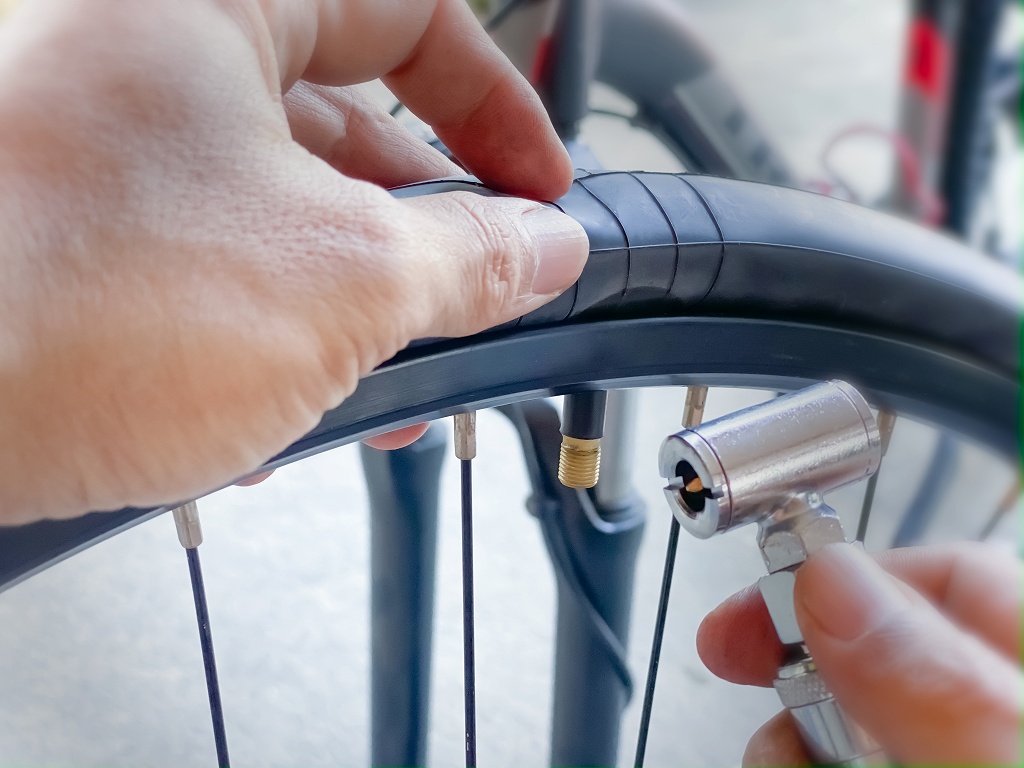
ウレタンゴム(U)
ウレタンゴムはゴム弾性をもったポリウレタンのことで、合成ゴムの中で最も耐摩耗性に優れています。この特徴からキャスターや制振材、シーリング材などに用いられています。
・長所
耐摩耗性や機械的強度に優れ、高いエネルギー吸収性をもつ
耐油性に優れる
・短所
耐熱性、耐水性に劣る
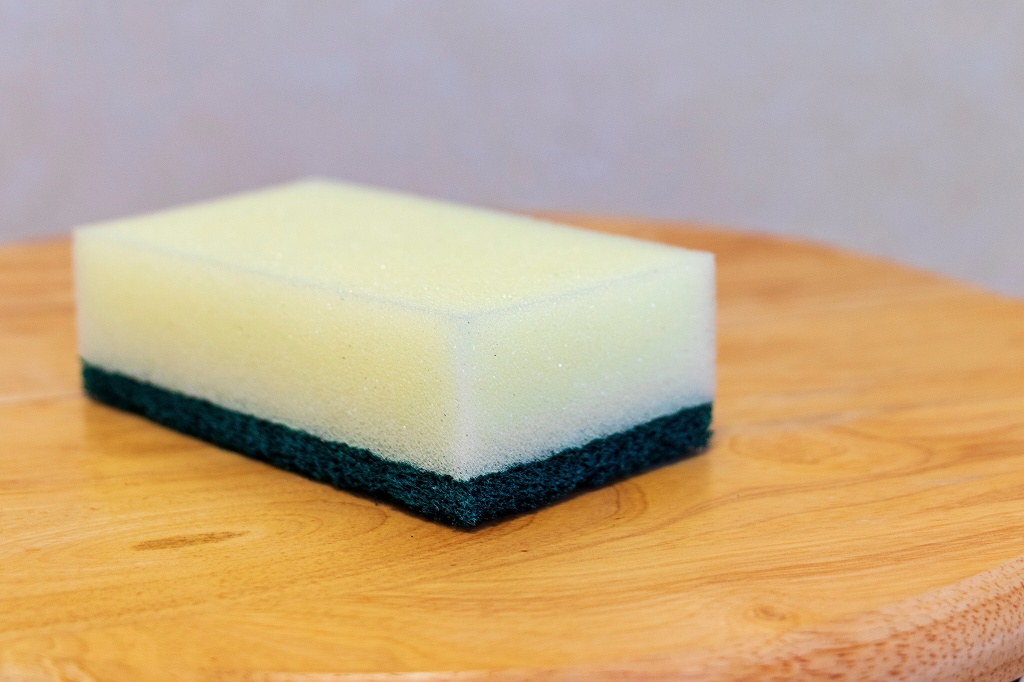
クロロスルフォン化ポリエチレンゴム(CSM)
CSMはポリエチレンを塩素化及びスルホン化してゴム弾性を持たせたもので、比較的自由な着色が可能という特徴を持ちます。耐熱性や耐候性に優れており、電線やゴムボート、ガスホースなどに使用されています。
・長所
耐熱性、耐薬品性、耐候性に優れる
自由な着色が可能
・短所
耐寒性に劣る
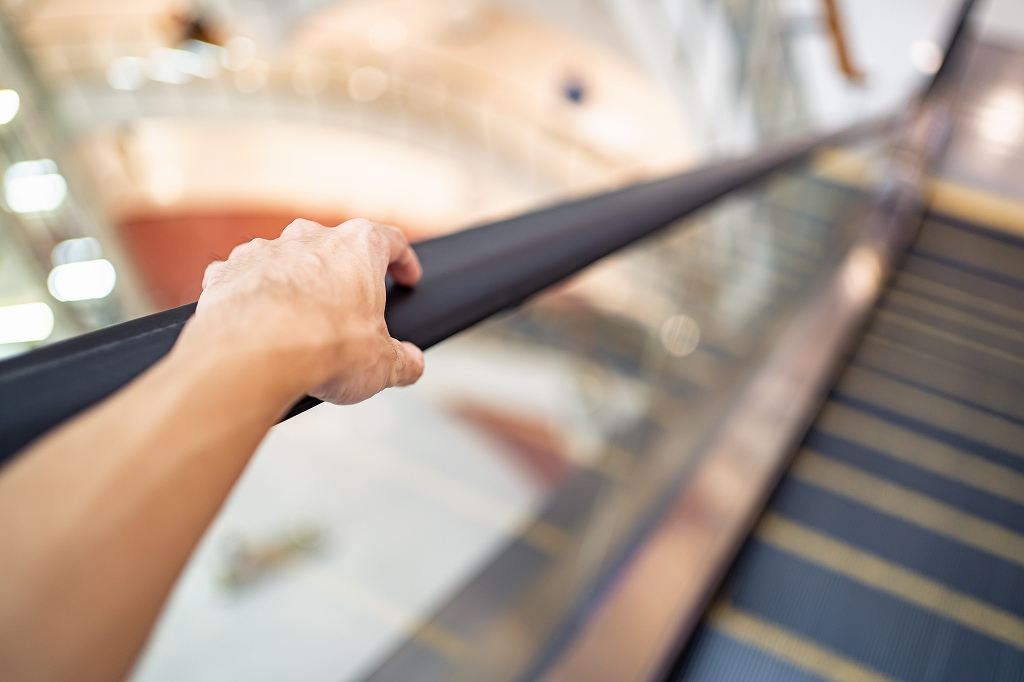
スチレンブタジエンゴム(SBR)
SBRはスチレンとブタジエンの共重合によって製造され、合成ゴムの中で最も多く生産されているゴムです。NRとのブレンドなどでタイヤに使用されているほか、防振ゴムにも用いられています。
・長所
加工性が良く、安定した物性を示す
耐摩耗性に優れる
・短所
構造に二重結合を持つことから耐熱性、耐候性が悪い
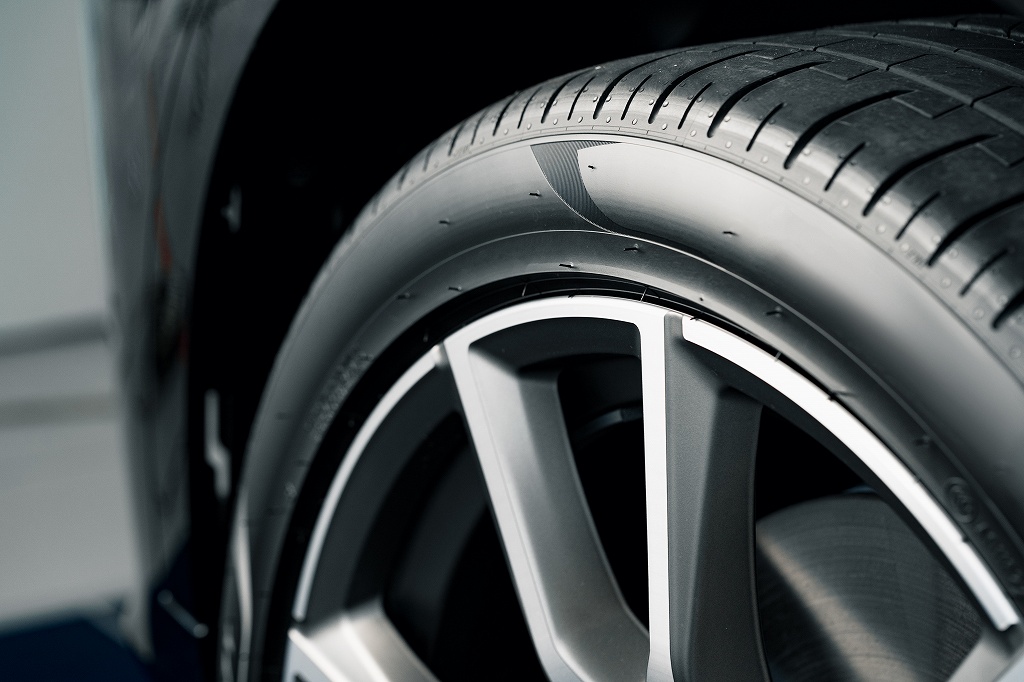
フロロシリコーンゴム(FVMQ)
イソプレンゴム(IR)
天然ゴムはゴムの木の樹液からできていますが、石油からできている天然ゴムに最も近い合成ゴムがイソプレンゴムになります。天然ゴム中に含まれるタンパク質が皮膚アレルギーを発症させるケースがありますが、それを含まないため健康被害が生じ難いのが特徴です。
・長所
皮膚アレルギーを起こし難い、においが少ないなどが天然ゴムより優れている
・短所
天然ゴム同様に耐熱性、耐オゾン性、耐油性などが劣る。天然ゴムよりも材料コストが高い
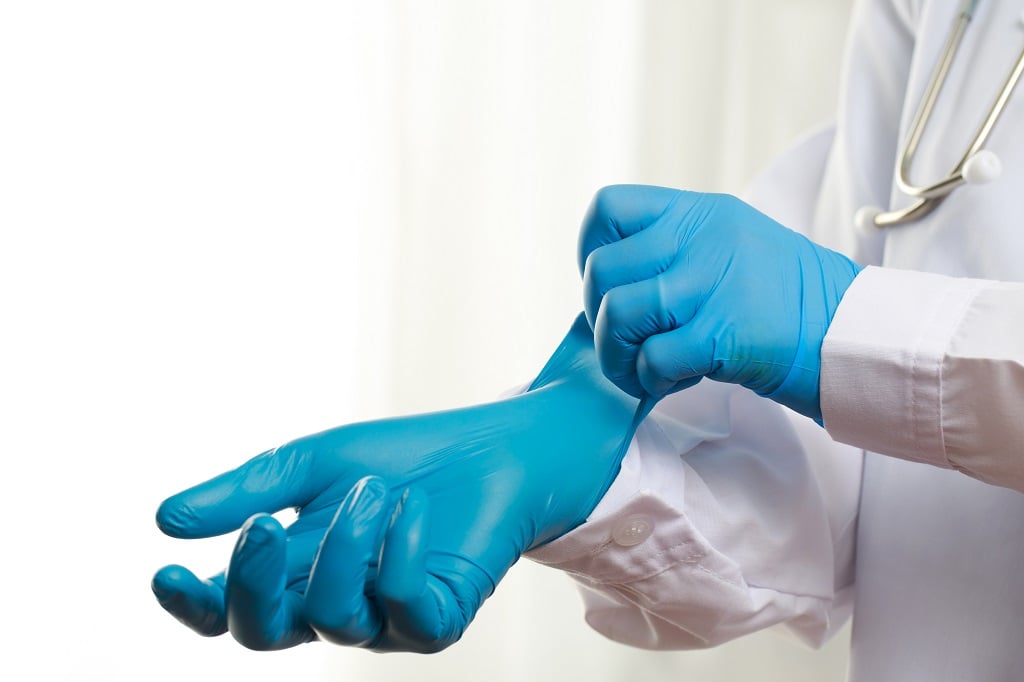
ブタジエンゴム(BR)
ゴムの中では最も弾性があります。良く弾む玩具のスーパーボールもこの材質が使用されています。他の用途ではタイヤなどに天然ゴムやSBRにブレンドして使用されます。
・長所
高反発弾性、摩耗性に優れる
・短所
耐オゾン性、耐油性、耐熱性が劣る
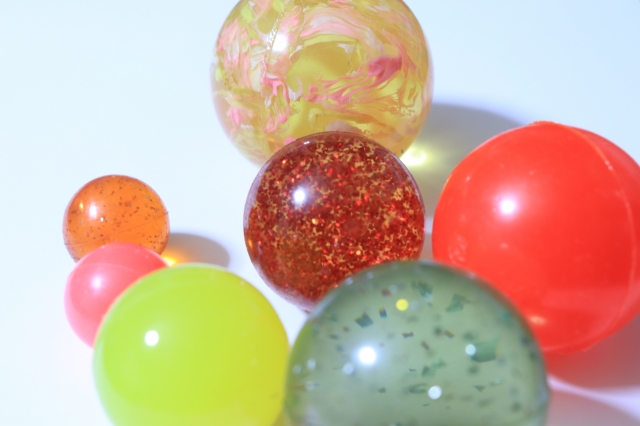
エピクロロヒドリンゴム(CO・ECO)
エピクロロヒドリンゴムはエピクロルヒドリンゴムと呼ばれる場合もあります。エピクロロヒドリンゴムの特徴から自動車用燃料系ホースに多く使用されています。他のゴム材質よりも電導性があるためOA機器の帯電ロールなどの使用用途もあります。
・長所
耐候性、耐オゾン性、ガス不透過性、耐油・耐ガソリン性に優れる
・短所
ケトンやエステル系の溶剤の耐性、他のゴム材質に比べて加工性が劣る

ゴムの種類一覧表
◎:優 〇:良 △:可 ×:不可
ゴムの種類と略号 |
天然ゴム |
イソプレンゴム
|
ブタジエンゴム
|
スチレンブタジエンゴム |
ニトリルゴム |
フッ素ゴム |
エチレン・プロピレンゴム |
ブチルゴム |
クロロプレンゴム |
クロロスルホン化ポリエチレン |
アクリルゴム |
シリコーンゴム |
ウレタンゴム |
エピクロロヒドリンゴム |
||
機械特性
|
実用硬度範囲 |
20~100 | 20~100 | 30~100 | 30~100 | 30~100 | 60~90 | 20~90 | 20~80 | 30~90 | 50~90 | 40~80 | 20~90 | 50~100 | 30~100 | |
引張強さ(MPa) |
3.0~30.6 | 3.0~20.4 | 3.0~20.4 | 3.0~20.4 | 3.0~20.4 | 7.0~15.3 | 3.0~20.40 | 3.0~15.3 | 3.0~25.5 | 3.0~20.4 | 3.0~12.2 | 4~10 | 15.3~45.9 | 5.1~19.3 | ||
反発弾性 | ◎ |
◎ |
◎ |
〇 | △ | △ | 〇 | △ | ◎ |
〇 | △ | ◎ |
◎ |
○ | ||
耐摩耗性 |
|
〇 |
|
〇 |
〇 |
〇 |
〇 |
△ |
〇 |
〇 |
〇 |
△ |
|
○ |
||
電気・物理的特性 |
電気絶縁性 |
|
|
|
|
△ |
〇 |
|
|
〇 |
〇 |
△ |
|
〇 |
△ |
|
対候性 | △ | △ | △ | △ | △ | 〇 | ◎ |
◎ |
〇 | ◎ |
〇 | ◎ |
〇 | ◎ | ||
耐オゾン性 | △ | △ | △ | △ | △ | 〇 | ◎ |
◎ |
〇 | ◎ |
〇 | ◎ |
〇 | ◎ | ||
耐熱
|
断続 |
120 | 120 | 120 | 120 | 130 | 260 | 150 | 150 | 130 | 150 | 190 | 230 | 80 | 150 | |
継続 |
70 | 70 | 70 | 70 | 90 | 200 | 110 | 110 | 100 | 110 | 150 | 170 | 70 | 110 | ||
最低使用温度(℃) |
-40 | -40 | -40 | -40 | -20 | -20 | -40 | -40 | -20 | -20 | -10 | -80 | -20 | -40 | ||
耐ガス透過性 | △ | △ | × | △ | 〇 | ◎ |
× | ◎ |
〇 | ◎ |
〇 | × | 〇 | ◎ |
||
耐油・耐薬品特性
|
耐水性 | 〇 | 〇 | ○ | 〇 | 〇 | ◎ |
〇 | ◎ |
〇 | ◎ |
△ | 〇 | △ | 〇 | |
耐油、ガソリン性 | × | × | × | × | ◎ |
◎ |
× | × | 〇 | 〇 | ◎ |
〇 | ◎ |
◎ |
||
耐動植物油性 | 〇 | 〇 | ○ | 〇 | ◎ |
〇 | 〇 | ◎ |
〇 | 〇 | ◎ |
〇 | 〇 | ◎ |
||
耐溶剤性
|
脂肪族系 |
× | × | × | × | ◎ |
◎ |
× | × | 〇 | 〇 | ◎ |
△ | 〇 | ◎ |
|
芳香族系 |
× | × | × | × | △ | ◎ |
× | × | × | × | × | × | × | △ | ||
ケトンエステル |
△ | △ | △ | △ | × | × | 〇 | 〇 | × | × | × | △ | × | × | ||
耐酸性 |
弱酸 |
〇 | ○ | ○ | 〇 | 〇 | ◎ |
◎ |
◎ |
〇 | ◎ |
△ | ◎ |
△ | 〇 | |
強酸 |
△ | △ | △ | △ | △ | ◎ |
◎ |
◎ |
〇 | ◎ |
△ | ◎ |
× | 〇 | ||
耐アルカリ性 |
〇 | ○ | ○ | 〇 | 〇 | △ | 〇 | 〇 | 〇 | 〇 | △ | △ | × | 〇 |
参照:日本ゴム協会東海支部(2010)『新板ゴム技術のABC 第2版』p.185 社団法人 日本ゴム協会東海支部
一般的な配合のデータであり、配合によっては異なったデータとなる
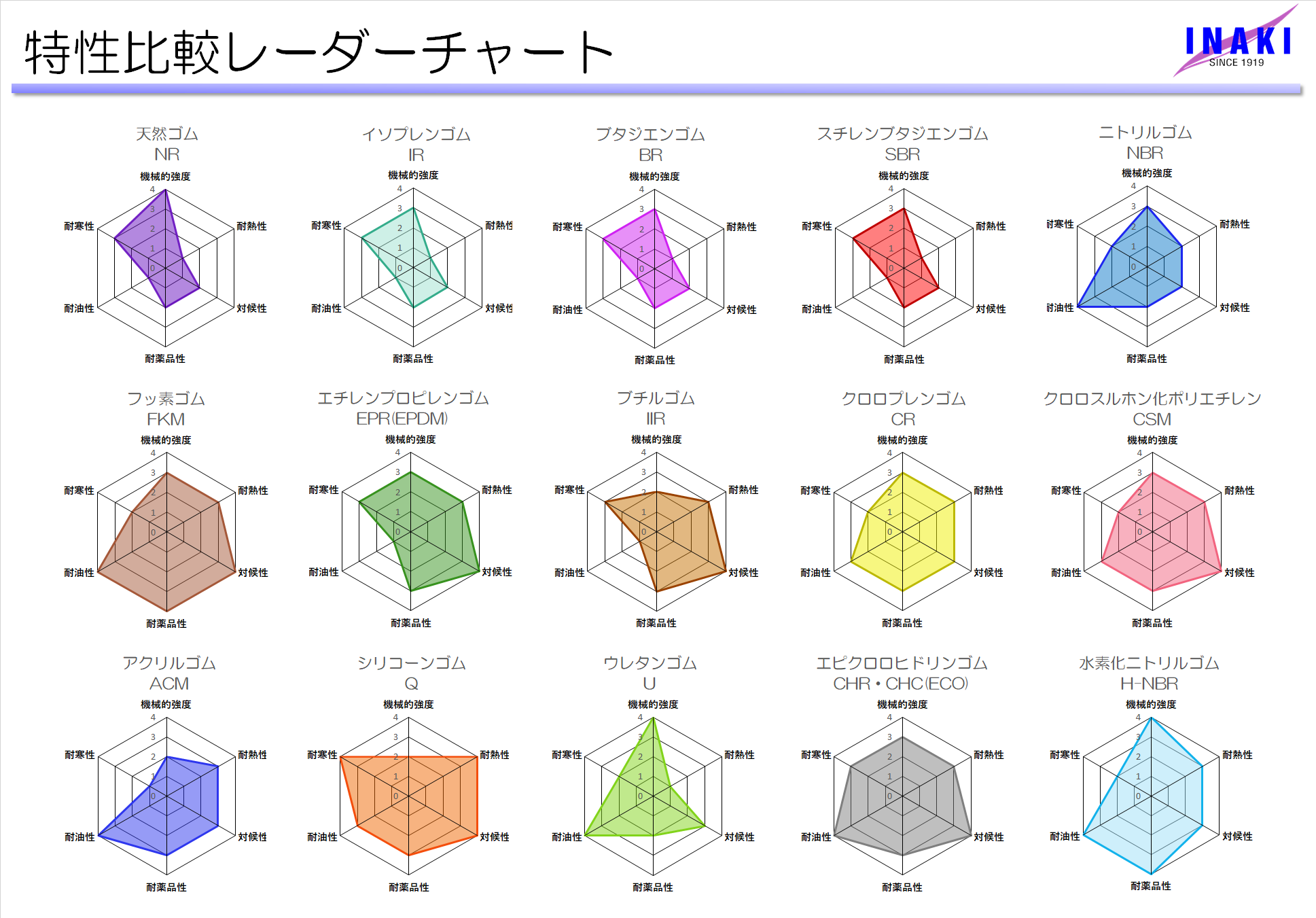
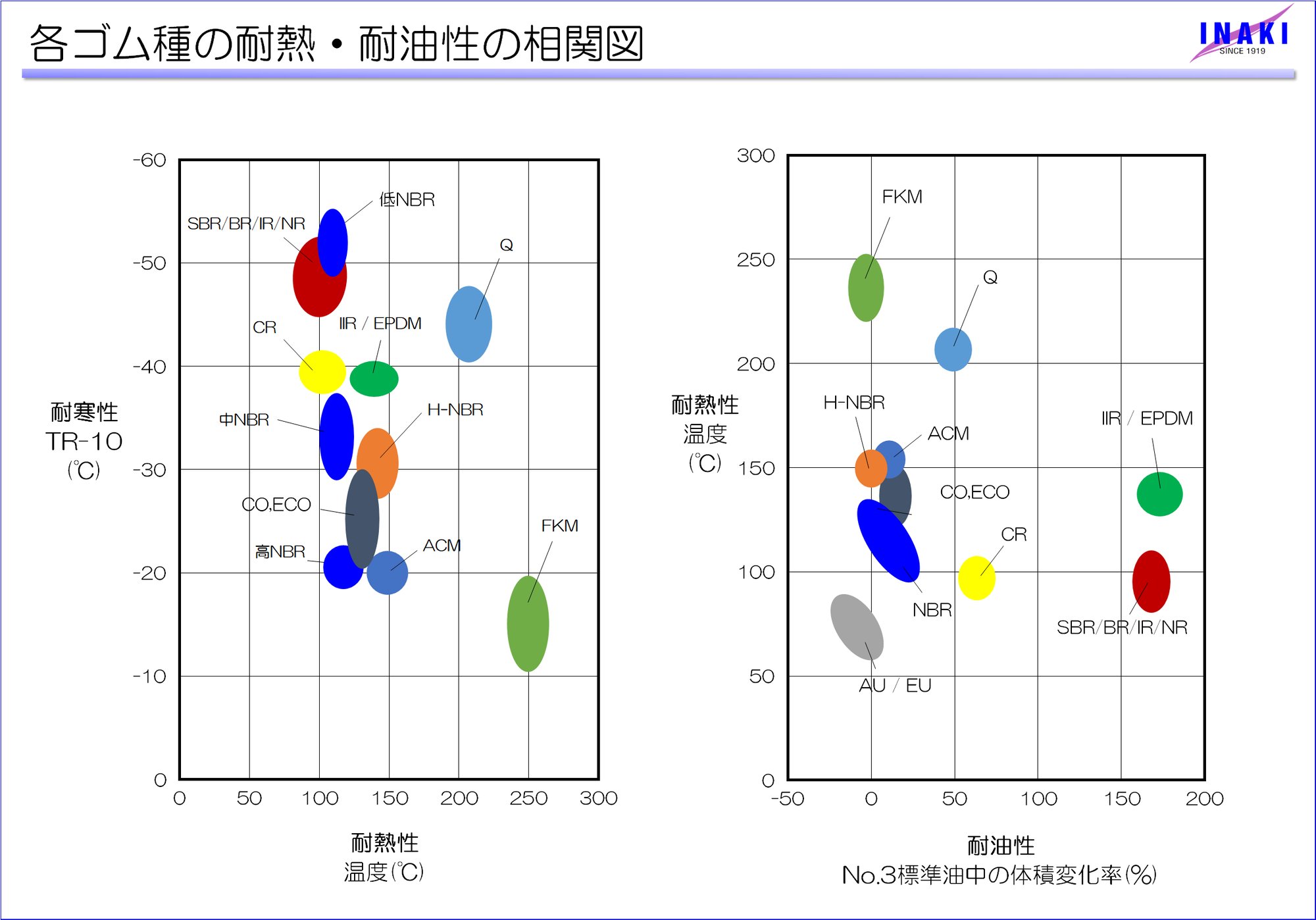
目的に合ったゴムの材料選定のポイント
ゴム材料の選定については、製品が使用される環境条件(耐熱性、耐寒性、耐油性、耐薬品性、耐候性、耐ガス透過性など)により適正なゴム材質の選定が必要になります。
注意が必要なのは、どのゴム材質も特性に一長一短があるため、要求される特性(コストも含む)のバランスに優れたゴム材質の選定が必須です。同ゴム材質でも配合設計(ポリマーグレード、補強材、フィラー、加工油、老化防止剤、加硫剤、加硫促進剤など)によりゴム硬さ、強度、圧縮永久ヒズミ性、電気絶縁性、その他の特性も変わります。
弊社では数百にのぼるゴム配合を有しており、その中から使用用途に合ったゴム材料を選定しています。
目的に合ったゴムの材料選定の事例
飲料用の水道管内に使用するゴムパッキン材の選定
ゴム材質はEPDMが主流です。他にNBR、H-NBR、VMQ、FKMなども使用温度や要求寿命により使い分けされています。水道管の蛇口や継手に使用されるゴムパッキンなどのゴムに触れた水道水が人の口に入る場合は、どのゴム材質も食品衛生法に適合している材料の選定が必須です。食品用器具・容器包装については、安全性を評価した物質のみを使用可能とするポジティブリスト制度が導入されています(令和2年6月1日施行)。水回りに使用されるゴム製品は、水による膨潤や水道水中の残留塩素により劣化を生じます。水道水による劣化は地域差があり、水道水中の残留塩素濃度が高い地域ほど劣化が促進し、水道水中に黒いゴムの欠片が混入する不具合が発生します。ポリマー材質、副資材の選定によりこの耐性は大きく変わります。水回りに使用する場合は特殊な配合設計をしています。
電気絶縁性のあるゴムの選定
ゴムは電気を通すでしょうか?通さないでしょうか? 「ゴムは絶縁体のため、電気を通さない。」と回答される方も多いと思います。一般的にゴムは絶縁体と言われていますが、「ゴムで絶縁できずにトラブルを生じた。」となるケースが実は多いのです。ゴムは原料ゴム(ポリマー)の他にカーボンブラックが一般的に添加されています。原料ゴムだけでは強度が低いため、補強性や硬度調整を目的にカーボンブラックが添加されていますが、このカーボンブラックは電気を通しやすい性質を持っています。このカーボンブラックのグレード・添加量により半導電領域~絶縁領域の電気特性を有することになります。導電性カーボンブラックや金属粉末の添加により導電領域レベルへの配合設計も可能になります。電気絶縁性が必要な場合はこのカーボンブラックの代わりに電気が通りにくいフィラーを選定した配合設計をしています。
ソルベントクラックを起こさないゴムの選定
ゴムと接触している樹脂がクラックを生じるケースがあります。特にゴム材質・NBRと非晶性樹脂(ABS、ポリカーボネートなど)の組み合わせでトラブルが発生しやすいため注意が必要です。この原因の殆どがNBRの配合添加物であるエステル系可塑剤です。非晶性樹脂に接触させてNBRを使用したい場合は耐ソルベントクラック性のNBR材料を選定する必要があります。